IoT Automation Empowers Engineers
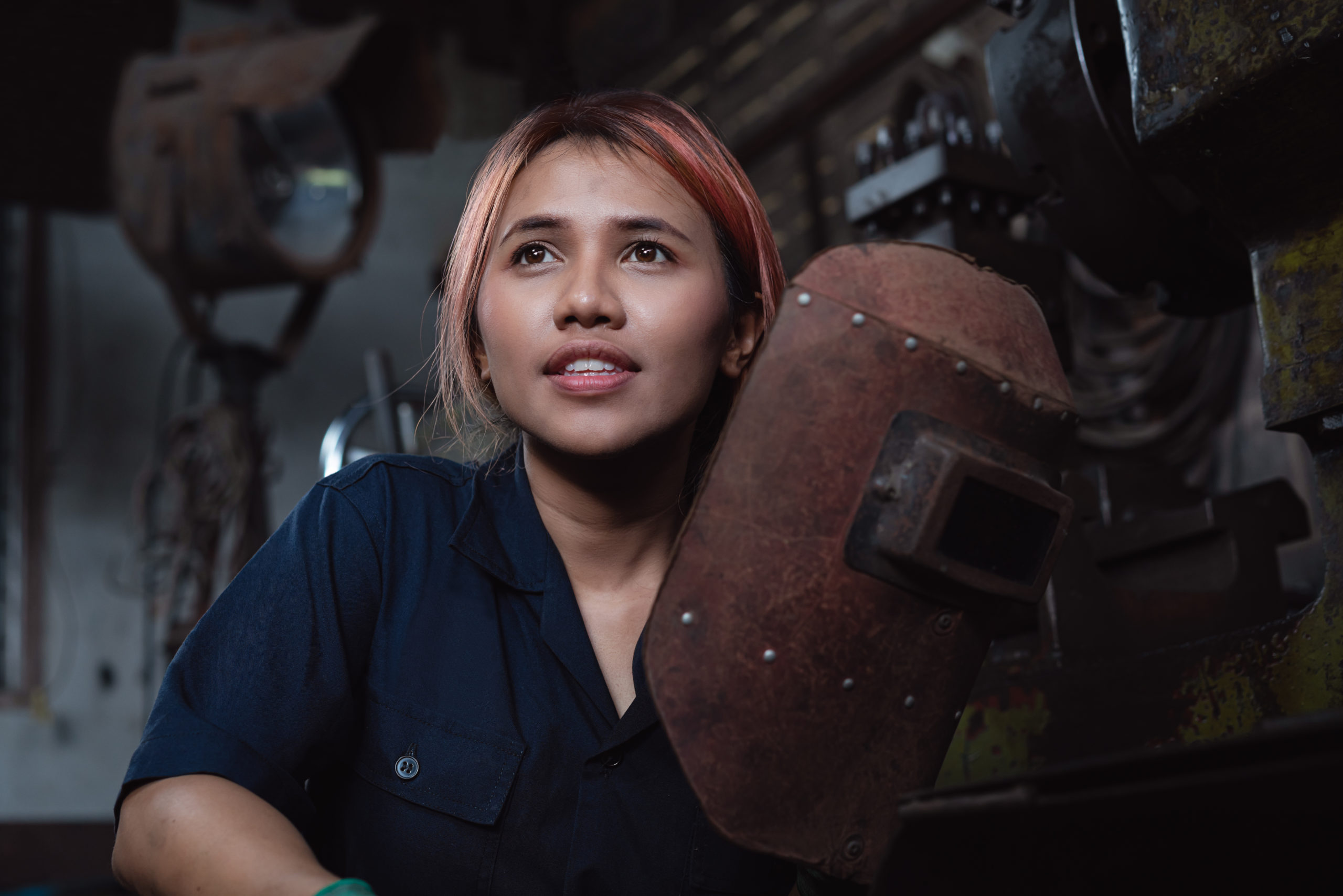
IoT advances are automating the assembly line, with long-term gains to a plant’s profitability and sustainable operations goals. As a result, plant managers see beneficial outcomes across the industrial manufacturing spectrum, including refining, packaging, welding, and beyond.
Part 2: IoT Use Cases Are on the Rise
As an engineer or plant manager, do you wish you had more time and more staff to optimize your factory’s operations? The answer lies in using the Internet of Things (IoT) for process automation, which empowers engineers to operate their factories more efficiently, while adding control capabilities to the workforce. As a result, plant managers see beneficial outcomes across the industrial manufacturing spectrum, including refining, packaging, welding, and beyond.
But how exactly does this capability tangibly transform industrial manufacturing, and what do you need to know to get started? The answer starts in our first blog of this ongoing series, where we discussed how process industries use IoT to monitor and control their assets remotely. The next step lies in understanding the value of automating IoT systems within the industrial manufacturing process.
According to IoT Analytics’ 2021 IoT Use Case Adoption Report, companies continue to augment manual and outdated automation setups. They are upgrading to brand new hardware and software that will help align their operations to changing customer requirements and evolving market needs. These upgrades include IoT systems that enable greater operational responsiveness with less hands-on involvement from their engineers. Operators (and their managers) can now adjust steps in their process as needed, freeing engineering teams to work on high-value projects that drive greater efficiency and energy savings. This adaptability is vital to retaining a competitive edge.
The Secret Sauce Behind IoT Process Automation
As defined by IoT Analytics, IoT-based process automation uses real-time data from connected assets to improve multiple parts of a manufacturing process. Some foresee process automation as eventually taking full control of an entire manufacturing facility. But most industry leaders (including Kelvin) think that process augmentation is a more realistic goal in the near term.
IoT-based process automation goes beyond traditional process automation systems by:
- Allowing you to choose independent control systems, sensors, and network components thanks to hardware-agnostic capabilities.
- Providing computing and communications power beyond the limited features and functionalities of your device manufacturer or software provider.
- Linking operations across multiple sites for more harmonized workflows and optimized performance.
Industrial automation is all about intelligent process control. Why send your plant manager down to the assembly line to flip a switch when an IoT-enabled controller can do it instead?
IoT takes the control concept further for additional optimization gains. The plant’s leadership team doesn’t need to stop programming the network to flip the switch and wait for the next scheduled event. Instead, the plant manager and engineering crew can use the system to observe how the assembly line responded to the change. If process throughput or energy usage improves, these enhancements can be implemented on other assembly lines for greater process gains across the plant.
Top 3 Ways IoT Powers Automation Projects
Industrial automation routinely diverts technology from the commercial sphere and adapts it to build new capabilities and competencies. The industry’s widespread IoT adoption builds upon this proven concept in numerous ways, yet three main features highlight the potential of IoT automation.
Wirelessly improving monitoring and control systems
Wireless connectivity removes many of the limitations of wired networks. For instance, it’s a challenge to use wired networks to link remotely controlled cranes or robot arms. Wires must be properly configured to accommodate unique ranges of motion and exposure to harsh operating environments. Removing the constraints makes the implementation of complex control systems more efficient–in both remote and hazardous environments.
IoT’s wireless functionality lets enterprises replace standard hard-wired connections with fully enclosed, Wi-Fi-enabled transmitters. Such wireless upgrades are particularly beneficial for automation processes that require fine-tuning or ongoing adjustments. For example, you can achieve higher transmission speeds with Wi-Fi, without deploying your engineering and maintenance crews to replace miles of Ethernet cable.
Building factories that run themselves
When manufacturing output grows quickly, busy engineers and plant managers may struggle to keep up. Conducting business at a higher volume introduces unique risks, such as the potential for greater material waste, energy usage, or manpower requirements if a process problem arises. That’s why automated control and remote monitoring are so important.
There are several reasons industrial automation experts love IoT. IoT lets assembly lines stay on course during times of exponential growth. For instance, a company wanting to conserve resources might use an industrial sensor system to notify them when auxiliary production lines should be shut down. Or an enterprise relying on automated stock machines to transport replacement parts to workstations could employ a connected framework to initiate new deliveries–without waiting for approval from a line manager.
IoT also enables the creation of digital twins–virtual replicas of existing, physical systems that serve as testbeds for new projects. A well-modeled digital twin dramatically simplifies project planning stages. If you were breaking ground for new facilities, for example, your digital doppelgänger could figure out how much floor space or equipment is required to deliver ideal output.
Managing real-time communications
For automation to be fruitful, real-time communications are critical. The earlier example of the switch-throwing manager exemplifies the hazards of lag. By the time the manager reaches the factory floor, the initial problem may have become irrelevant or much worse – prompting a lengthy and costly shutdown.
Workflow adjustments may be overlooked because they often go on in the background. But they are an essential part of ensuring that automation frameworks behave as intended. When your industrial communication systems behave consistently, you can execute sound management practices more efficiently.
How can IoT help your automation processes expand in sustainable ways?
As your manufacturing processes grow to meet new market demands, IoT can program automation functions at the node level. This helps optimize resource usage, including your energy spending and the use of your engineering teams. The net results include lower operating costs and a more productive enterprise.
The optimal IoT system is not one-size-fits-all. It’s defined by the circumstances. As a result, you need to map out and build your IoT system to be flexible, yet sufficiently robust to survive the unexpected.
Processing plants have pressing needs for IoT-enabled automation beyond just the bottom line. Compliance with health, safety, and environmental (HSE) regulations is also a critical metric. The cost of noncompliance can be extremely high, ranging from daily fines to plant shutdowns. Automated processes can help plants operate within predetermined HSE requirements–minimizing risks to their people and their surroundings.
Consider the adoption of IoT in welding applications. As Arc Machines Inc. states, the data that IoT systems capture from each welding job can be collected and analyzed to set a baseline for a safe, long-lasting weld. By comparing each subsequent welding job to this baseline, companies can ensure a high-quality weld that minimizes the risk of leaks or ruptures. And as more companies use semi-automated processes like orbital welding, IoT controls help take human welders out of the “hot zone.” If changes to a welding operation are required on-the-fly, the IoT system lets the operator make adjustments remotely.
As manufacturers face mounting challenges to optimize their operations on the assembly line, process automation will play an increasingly critical role. Ongoing advances in IoT-enabled automation promise greater process efficiency, sustainability, and safety both today and in the future.
Are your engineers empowered with the full capabilities of IoT-enabled automation?
Kelvin can help.
Kelvin’s leading sustainable operations software helps clients achieve their sustainability goals and reach new levels of business excellence. Combining human intelligence and machine learning, our event detection and workflow automation solutions help businesses optimize their sustainable operations efficiencies, maximize performance and profitability, and minimize emissions and energy costs—a value-driven solution we call “The Kelvin Effect.”
Tapping into an integrated suite of software, engineers can boost manufacturing performance through Kelvin Maps for data visualization and simulation, Kelvin Copilot for application optimization and control, and Kevin Platform for asset management.
Want to learn how The Kelvin Effect can help you optimize your asset performance and meet your sustainability goals? Contact us today.