Three ways to future-proof your industrial control systems
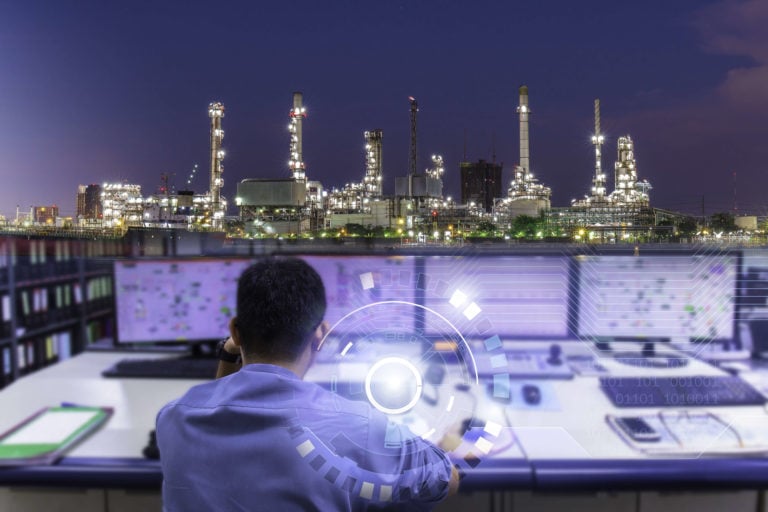
COVID-19 has significantly tested the industrial sector’s ability to navigate through disruptions. Pandemic-related shutdowns, new regulations, social distancing, and reduced global industrial activity force operators to upend their standard procedures overnight.
In the new post-COVID-era, it is clear that all manufacturers must begin adopting a ‘technology-forward’ approach to making their control systems more efficient and their operations fully autonomous.
Full autonomy may be far off for most operators, who are likely asking themselves, “Where do I start?” With technology developing so quickly, there is a concern that you may not make the right choice; and by the time you’ve adopted the ‘new and shiny’ thing into your operation, it’ll be obsolete.
There is no need to worry. While innovation may be outpacing your ability to adopt these new technologies fully, there are steps you can take today to help future-proof your control system for future innovation.
Traditional industrial control systems consist of proprietary machines and software, patched together using a framework of programs and workarounds that are difficult to reconfigure. Future-proofing your operation will require you to eliminate these challenges and optimize your systems to deal with disruptions.
We’ve identified three steps you can take today to move towards more future-proof operations.
1. Implementing standardized communication layers
Despite the standardization drive of the OPC Foundation, the availability of legacy equipment and proprietary hardware on every shop floor means industrial facilities still manage control processes using patched solutions.
Generally, when disruptions occur, or you need to add new equipment to your existing systems, in-house engineers manage any necessary workarounds. Custom workarounds often lead to an over-reliance on individual engineers and a reduced ability to respond to changes in real-time.
Standardized communication layers provide a more versatile solution to change management within your industrial control system. Adopting standardized communication layers means utilizing a system capable of interacting with all the assets on the shop floor– including legacy equipment. The standardized system is deployed between shop floor assets and information or network systems, thus serving as a supportive interface for diverse vendor-specific assets.
Standardized communication systems also benefit scalability when including new equipment or systems to existing operational technology architecture. The non-proprietary or open nature of standardized layers will easily support integrating additional assets using previously established processes. This provides your operation more flexibility as you test new software, systems, and procedures.
2. Adopting lean project management principles
Lean manufacturing has become a staple of the industrial sector with a proven track record of successfully improving productivity and reducing waste across the production line. The lean manufacturing principle focuses on eliminating complexities through a modular approach to building operational systems. Applying this modular approach to future-proofing industrial control systems allows you to expand your process control systems incrementally.
This expansion of control system capabilities is done by unchaining control applications from individual equipment and physical controllers and transferring networking to a centralized platform. Industrial enterprises that utilize the software and established protocols within these platforms can incrementally expand the capacity of an industrial control system.
Adopting a lean modular approach future-proofs industrial control systems by supporting expansion projects and limiting the effects of shutdowns. For example, after a shutdown, restarting the production line will not require reconfiguring a patchwork of I/Os, PLCs, and communication software. Instead, a restart can be automated by using the centralized platform to reconfigure I/Os, independently of individual controllers, assets, and subsystems.
The Lean modular approach also simplifies the process of adding new assets to existing process control systems. Facility engineers no longer need to develop new control strategies or redistribute I/O modules to add new assets. Instead, control applications are managed independently from the physical equipment using containerization.
Control application containers include features to allocate functionalities to individual assets and integrate them into existing infrastructure without executing complex system-level configurations.
3. Leveraging industrial software platforms
Industrial software platforms are a vital component required to build a future-proof control system. These platforms abstract away the complexity of connecting, creating, and scaling new process control applications onto your existing system.
Connecting to new software is often one of the most challenging parts of adopting a platform. Modern industrial software platforms are built on open-industrial standards like OPC, allowing them to automatically provide your system with a built-in standardized communication layer. Thus enabling your control system, assets, and technology to all easily connect and communicate.
Creating new applications can be challenging for an operator that does not have software development experience. Industrial software platforms provide a simplified, low-code environment that allows your SME to develop logic-based control applications without the need for a Ph.D. developer—significantly reducing the time and cost required to automate supervisory and routine tasks.
Scaling existing or novel control applications can also be very difficult for your operational teams. Industrial software platforms use containerization, which separates control applications from the underlying hardware, and modularizes it to run anywhere within your control system. Because each container includes everything it requires to run, it is easy to deploy and scale thousands of assets anywhere in the world.
The industrial software platform empowers enterprises to develop and deploy optimization techniques and Industry 4.0 business models to reduce waste and downtime while enabling interoperability.
For example, industrial automation enterprises can deploy Kelvin’s industrial control application platform to collect vibration data sets from shop floor assets and analyze aggregated data using industry-specific apps. AI-powered applications can detect anomalies from the captured data set that highlight individual issues within operational equipment. In this scenario, the industrial control platform becomes the foundation for developing predictive maintenance or condition monitoring strategies defined by Industry 4.0.
Conclusion
Future-proofing your control system involves integrating technological solutions and processes that eliminate the complexities of managing industrial control systems. Applying standardized communication layers and lean modular principles powered by industrial control platforms provides the industrial sector with excellent solutions to disrupt and implement Industry 4.0 business models.