What is Edge Computing and its Importance for IIoT?
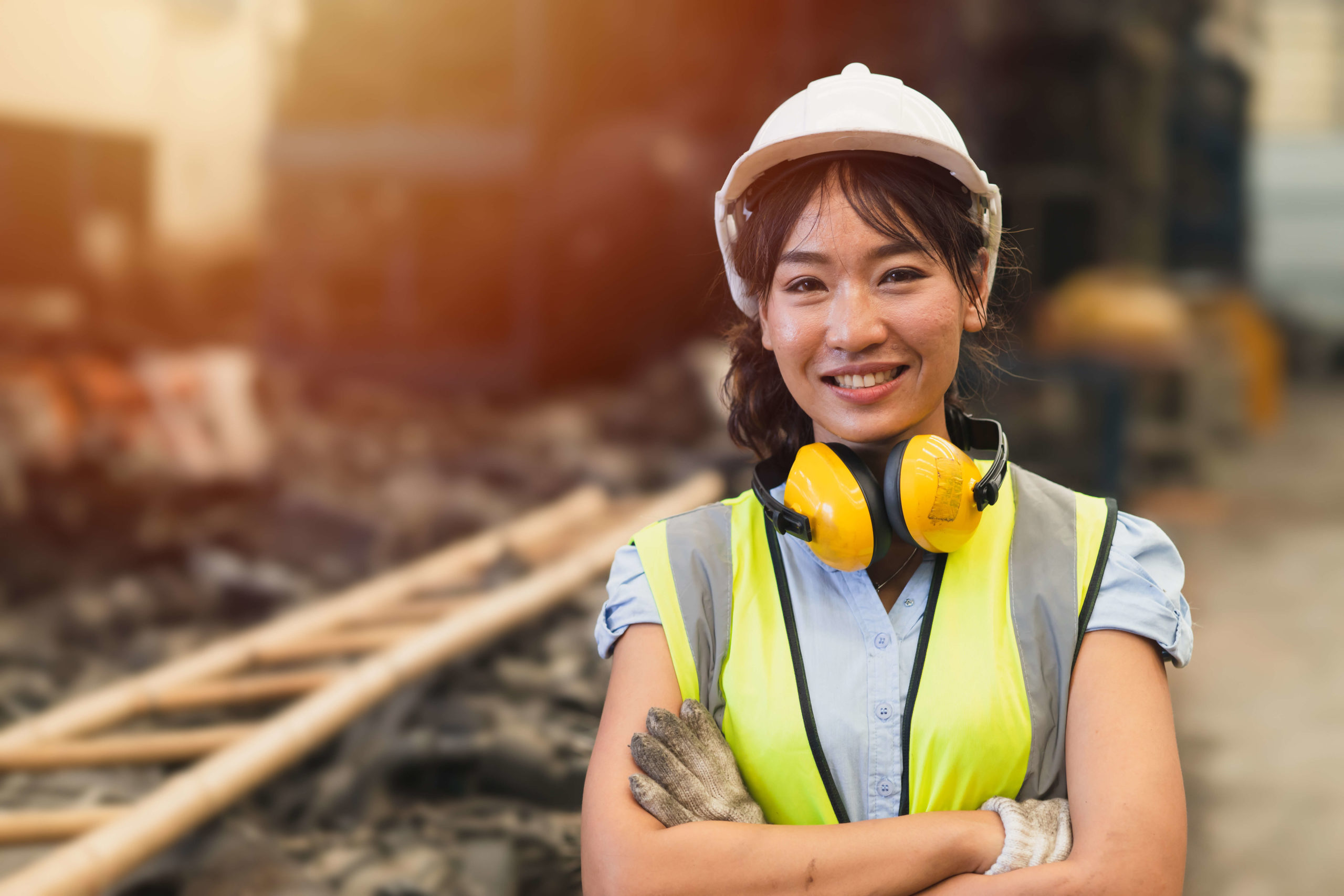
Part 2 of 2: What is Edge Computing and its Importance for IIoT?
This article is part two of our two-article discussion on edge computing and IIOT. The first can be found here.
As was previously mentioned in Part 1 of this series, the adoption of IIoT and Industry 4.0 practices have bolstered the development of industrial edge computing for manufacturers and operators in all industries. This article will dive deeper into what edge computing is, what it is not, and how it helps industrial operators innovate.
To begin, since many often ask, it may be helpful to clarify how edge computing differs from another concept popularly discussed in IIoT today: fog computing.
Edge Computing vs. Fog Computing
Edge computing and fog computing are slightly different but highly related processes. Like many emerging technologies, the definition of edge computing and fog computing often vary depending on which expert you ask.
For our purposes, edge computing is a form of distributed computing that occurs inside or physically close to the device. Edge computing is performed by IoT devices such as a ‘smart’ programmable logic controller (PLC) in a factory.
By contrast, fog computing refers to a decentralized computing structure where the processor connects within the local area network (LAN). In this case, the processor may not be physically close to the hardware itself. An excellent example of fog computing would be a ruggedized computer connected to an electric submersible pump (ESP) in an oil and gas field. The pump, located at the bottom of the oil well, is connected to the processor on the surface. Any compute needed to run the pump happens on the surface and is transmitted to the pump below.
Edge computing will be the focus of this article.
How Edge Computing for Industrial IoT Functions
An increasing number of organizations find edge computing appealing because it allows for increased function and optimization at a lower cost. But how does it work in practice? Let’s look at how operators are using edge computing on their shop floors to identify and predict the health of a compressor.
Compressors have dozens of applications in the industrial environment. Often, they are a critical component of a plant’s process.
Before edge computing, the raw operational data from the compressor’s vibration sensor was sent to the cloud to be processed and analyzed. Transferring raw and unprocessed data strained the plant’s network and cloud database.
Operators only had access to the process data after a significant delay and could not use it for real-time insights.
Edge computing enables the processing of the sensor data without sending it over the network. Once the data is processed, only important insights are sent to the cloud and operator in real-time—improving network performance and cloud database efficiency.
Real-time data analysis also enables operators to deploy advanced applications—like the Kelvin Asset Health Monitoring—on top of their existing automation. These applications take the processed data and provide predictive maintenance capabilities that alert operators when and why their equipment may fail in the future. Greater visibility into asset health decreases downtime and improves plant efficiency.
Applying Edge Computing for Industrial IoT
Edge computing for IIoT also involves finding ways to achieve low-latency computing in manufacturing processes. Many of these efforts have borne fruit and contributed to the advancements of edge computing in IIoT. The following are a few applications of these advancements.
Driving Automation
Complete integration of edge computing in processes, devices, and equipment that drive operations opens up ways to fully automate industrial shop floors. In cases where IIoT devices capture large datasets on the shop floor, sending these datasets to central servers in the cloud for analysis and then receiving actionable insights can make automation slow and costly.
The integration of edge computing eliminates the lag between communication and processing to facilitate real-time automation. With human intervention reduced, operators are then free to focus on higher-order tasks.
Automation of Maintenance Procedures
Smart facilities need to optimize and maintain IIoT devices to operate at peak capacity, so predictive maintenance of shop floors is one of the primary pillars of Industry 4.0.
Consequently, in addition to capturing data about the immediate environment, IIoT devices can self-diagnose and take corrective actions to ensure they function efficiently. And edge computing facilitates the complete automation of IIoT devices to aid in this effort.
For example, the resulting corrective actions may be as simple as running diagnostic checks and automatically recharging devices, and proactively changing the motor speed on one machine. Such automated activities enhance productivity and reduce downtime.
Advancements in IT Security
SMEs and large corporations in manufacturing face significant challenges when attempting to plug security loopholes in various IT systems. The introduction of IIoT to manufacturing has only exacerbated security problems because IIoT devices create multiple access points vulnerable to cyberattacks.
The application of edge computing for IIoT presents a significant opportunity for resolving these security challenges. Because edge computing allows all IIoT devices to operate independently, the number of access points or potential breach points is dramatically reduced. This benefit can also be applied to legacy equipment to create industrial shop floors that process all data locally.
As a result, legacy equipment and IIoT devices alike will capture and process all temporary data and send only permanent data to a centralized database. Therefore, edge computing for IIoT adds another layer of protection in an age when cyberattacks are becoming increasingly prevalent and sophisticated.
Endless Opportunities to Advance the Industrial Revolution
Technologies like edge computing and the IIoT are already transforming how manufacturers and industrial operators control their processes. Operators can now use edge computing to reduce costs, increase production, and strengthen the security of industrial operations. And this is only the beginning.
Advanced operators have even begun to use these new technologies to leverage machine learning to improve decision-making and automate routine actions to increase productivity.
As edge computing and IIoT technology continue to advance, the opportunities to the industrial automation industry will increase exponentially. And companies like Kelvin stand ready to help operators capitalize on improving compute capabilities with sophisticated applications that optimize automation, increase equipment uptime, and lower maintenance and operating costs.
If you are interested in learning more about how edge computing and advanced automation applications can help improve your operation, contact one of our edge computing experts at Kelvin.ai.
If you did not get a chance to read it, please find Part 1: Advantages of Edge Computing and What it Means to IIoT