5 Ways Manufacturers Can Build Factories of the Future
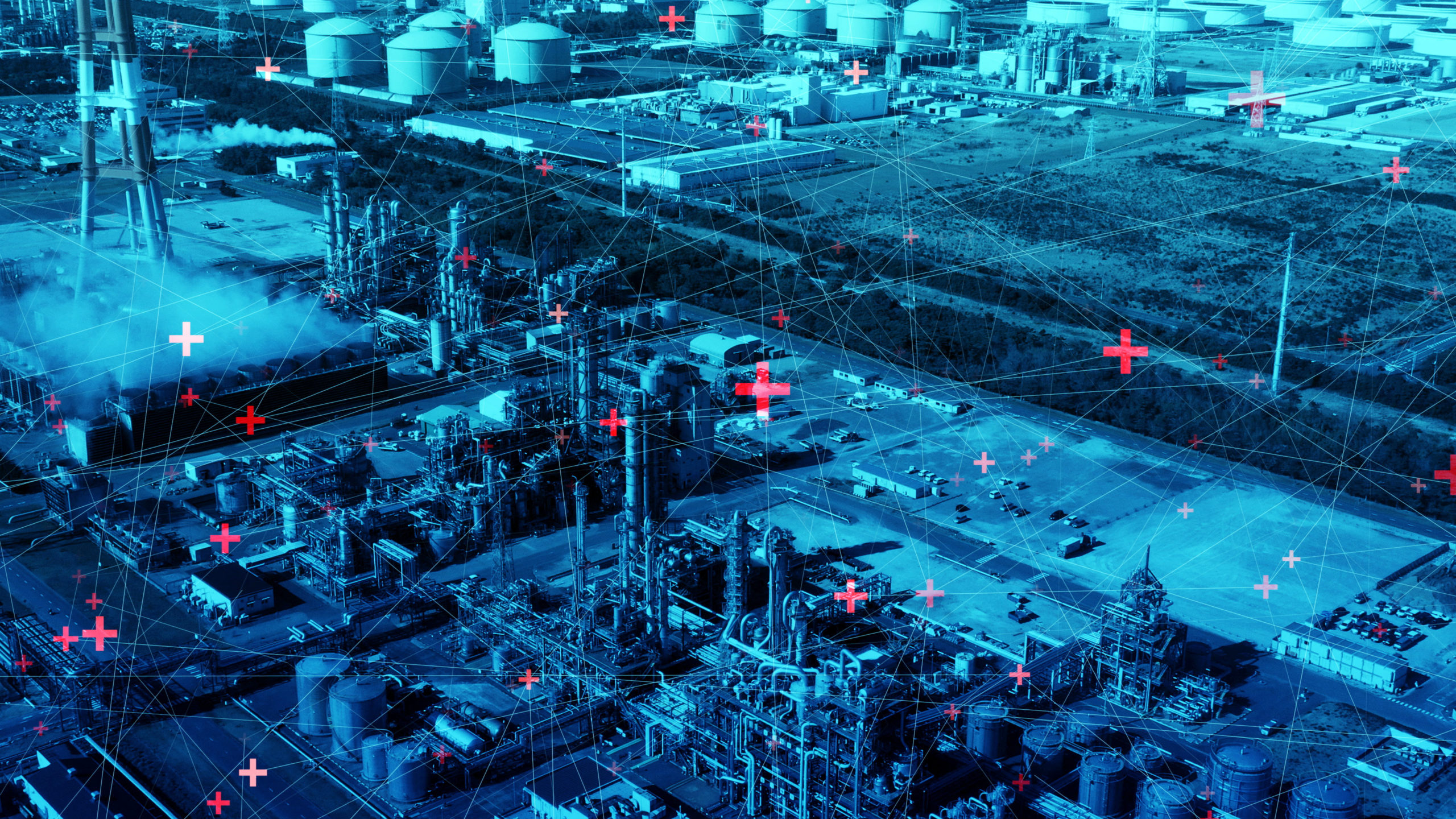
Automation and augmenting human intelligence are the keys to competitiveness for modern manufacturers. Here are five ways manufacturers can create the factories of tomorrow.
5 Ways Manufacturers Can Build Factories of the Future
There’s a business trend sweeping the world that, before we know it, will separate the innovative and cutting-edge factories of the future from those stuck in the past. This trend is propelled by artificial intelligence (AI) and machine learning (ML) making automation and augmentation possible, and it’s catapulting industries forward.
A global survey from McKinsey & Co. found that AI adoption remains on the rise, as 56% of all respondents report artificial intelligence adoption in at least one function, up from 50% in 2020. And two business functions where AI adoption is most common are service operations and product and service development.
In manufacturing, this is particularly relevant. Research from Google Cloud found that 76% of polled senior manufacturing executives across seven countries have turned to digital enablers and disruptive technologies to respond to the pandemic. These technologies include data analytics, cloud, and AI.
Not only do the leaders now rely on these tools more, but adoption is keeping them globally competitive and well-equipped for when the next innovation comes around. It’s about planning for tomorrow while making operations more efficient, cost-effective, and streamlined.
Below are five ways manufacturers can build factories of the future:
1. Integrate IT/OT Systems and Embrace Automation
As manufacturers continue to digitally transform legacy systems and processes, a path is paved to adopt and deploy helpful automation tools. Integrating information technology (IT) and operational technology (OT) systems means various teams can collaborate, access data, and communicate to speed up operations and production processes.
Once data previously trapped in siloed environments is connected, workflows can be automated across the industrial complex. Engineers and managers can deploy automation applications to:
- Optimize plant operations
- Streamline mundane tasks and processes
- Analyze sensor data
- Speed up time to insight
- Automate control systems and more
Domain experts can even leverage their knowledge to build applications that detect certain events and disseminate those insights across the enterprise for better visibility, productivity, and sustainability.
2. Adopt Predictive Maintenance
By leveraging automation capabilities, manufacturers can tap into predictive maintenance to prevent equipment failures before they happen and automate corrective actions. Rather than fixing equipment after it malfunctions, smart manufacturers use sensor data to obtain predictive insight on asset performance and plant operations down to the component level.
Receiving event detection and anomaly insights will save time and money, and automation capabilities enable seamless corrective actions at scale. Plus, relying on performance and sensor data processed where it originates reduces latency, making systems faster and more reliable.
Imagine your best engineer on-site 24/7, watching all equipment and responding to any issues whenever they occur – that’s the art of the possible with predictive maintenance.
Predictive analytics opens the door to failure mapping. Tools like failure mode analysis software can detect equipment failures and production losses, saving plants from expensive breakdowns and shutdowns. These capabilities include condition-based monitoring to control assets in real-time and prescriptive analytics that can help prevent failures before they happen. More advanced software allows managers and their staff to customize monitoring for their factory’s unique processes, equipment, and defects.
3. Augment Human Intelligence with IoT
Manufacturers of the future aren’t replacing people with technology. Instead, they’re augmenting human intelligence with automation tools, Internet of Things (IoT) devices, and enhanced capabilities – and for a good reason.
To leverage a platform that analyzes data from IoT devices, an organization must first securely deploy and use those devices. This is where the power of edge computing comes into play. An advanced internal operating system safely connecting to data sources will also connect to smart assets and sensors generating meaningful data.
Similar to gaining insights from predictive analytics, engineers and leaders on staff will receive data analysis from all IoT devices verified to connect to the organization’s network. This real-time connectivity significantly slashes risk as data agilely translates into actionable insights, and the IoT infrastructure delivers measurable ROI. Manufacturers can spend more time making data-driven decisions and less time gathering and analyzing the data manually.
4. Optimize Operations with AI and Machine Learning
The future of most industries is undoubtedly in AI and ML. This type of connectivity and intelligence equates to enhanced process control for manufacturers. And considering the complexity of manufacturing operations, AI must be orchestrated so multiple automated tasks create a seamless dynamic workflow.
Kelvin’s collaborative control software, for example, connects hundreds of machines across a manufacturer’s existing platform to create that dynamic workflow. It’s also the foundation of custom application creation, with controlled decision-making that provides maximum visibility into data insights and detection capabilities.
And with AI, ML, and advanced algorithms, a machine can even learn and adopt human behavior, according to Forbes. This translates into data collection, performing skilled labor, and even predicting consumer behavior. “Smart factories with integrated IT systems provide relevant data to both sides of the supply chain more easily, increasing production capacity by 20%,” writes Forbes. “Quality is no longer sacrificed for efficiency, as machine learning algorithms determine which factors impact service and production quality.”
In terms of resources, Forbes reports that digitizing the manufacturing industry means less wasted time and materials, lower cost of production, and quicker turnarounds to meet customer needs.
5. Improve and Innovate Using Data Insights
Gathered insights from data in real-time are extremely valuable for on-the-spot decision-making. Data can also be beneficial for preparing for the future. Manufacturing leaders can iteratively plan for and implement improvements and innovations using analyzed data from ROI reports, performance metrics, usability studies, events, and components.
In addition to collecting KPI data that drives process improvement and production efficiency, future manufacturers will need insights into sustainable operations. Environmental, Social, and Governance (ESG) regulations and net-zero goals will continue to be important. Industrial facilities that automate workflows are already seeing battle-tested results, including reduced emissions and energy consumption.
Ready to build your factory of the future?
Kelvin can help.
In sum, digital transformation is a multi-level journey. Manufacturers need partners to build their factories of the future, and Kelvin has the technology to level them up.
Kelvin can help you bring your automated, smart factory from a dream to a reality, partnering with you in these five pivotal steps:
- Embracing automation with technology that bridges the gap between IT/OT and paves the way for workflow automation.
- Adopting predictive maintenance and monitoring assets to improve safety and reduce bottlenecks at your plant.
- Augmenting human intelligence with IoT and turning your data into a Copilot application that codifies your own best practices.
- Optimizing operations with AI and machine learning and leveraging your Copilot application for edge-to-cloud closed-loop control.
- Improving and innovating using data insights that boost both productivity and sustainability.
Combining all these capabilities will help you stay on the bleeding edge of tech. Although the future is a moving target, your factories will be well-equipped to adapt to new challenges with smart tools from Kelvin.
To learn more about how Kelvin.ai helps customers reduce emissions and hit Net Zero goals — while boosting production and efficiency, contact us today.