Closing the Loop between Insights & Action
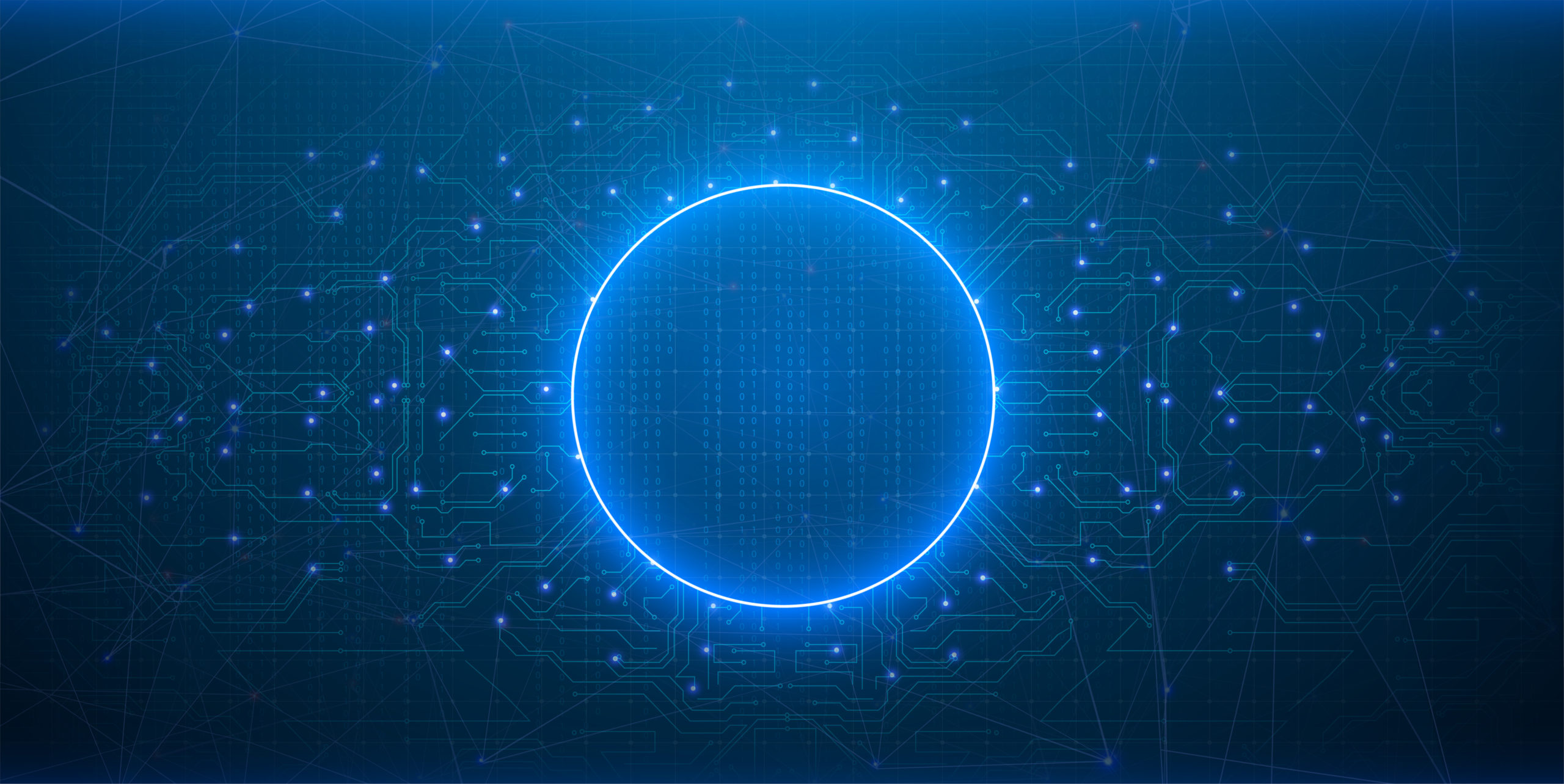
Moving past the unidimensional data analysis associated with open-loop control systems allows system errors and broken processes to be fixed quickly and efficiently. Every second matters on the production line and in a factory, plant, or field site. This is where closed-loop feedback control systems show their value.
Closing the Loop between Insights & Action
In today’s world of big data, where roughly 2.5 quintillion bytes of data are generated every single day, it’s not the size of your data that matters. It’s how you use it. We’re in information overload, but that information can be extremely useful – if we extract valuable insights at the point when they most matter and let those insights work for us. Closed-loop control does exactly that. It closes the loop between data insights and automating actions in industry.
Moving past the unidimensional data analysis associated with open-loop control systems allows system errors and broken processes to be fixed quickly and efficiently. Every second matters on the production line and in a factory, plant, or field site. This is where closed-loop feedback control systems show their value.
The biggest difference between closed-loop and open-loop systems is feedback. Wikipedia explains that in an open-loop system, control actions are not directly linked to a desired outcome. For example, if a boiler in a central heating system is being controlled by a timer with no connection to the temperature inside the building that it’s heating, then you have an open-loop control system.
When it comes to Internet of Things (IoT) systems, this means that devices using open-loop control aren’t configured to provide any feedback or data processing. Instead, they may simply take readings and send those results to a central repository. Afterwards, much of that data can be manually analyzed against whatever parameters users feel are important. The inefficiencies of a system like that can include a long delay between when readings are taken and the analysis of that data. Depending on the complexity of the system, reports can take a week or more to manually produce, in which case, the findings may be outdated and unusable.
Open-loop control systems aren’t efficient because there’s no built-in feedback completing the cycle. There’s nothing automatically telling the system what to measure or how to stay within a setpoint configuration. Open-loop control actions are independent from the process output, notes Wikipedia. This means that your data doesn’t connect back to the system to produce your desired outcome. It’s a one-sided process.
Take Closed-Loop Control with Kelvin AI
Kelvin AI is closing that loop to not only provide data insights, but to make them actionable in real-time. In a closed-loop control system, Wikipedia states there’s an algorithm governing the application of inputs, which in turn drives the system toward a defined purpose. The system knows what to measure, with less overshooting or delay.
Continuing with the boiler example cited above, a thermostat compares the building’s temperature with a set point on the thermostat and the system stops heating when registering target temperature. On the other side, having the building get too cold could trigger the boiler to come back on, heating things up until the building once again falls within the desired temperature range.
Ultimately, closed-loop control systems improve both efficiency and productivity. It’s like when your smoke detector triggers the emergency sprinklers at the first sign of trouble. This happens instantly, not a week later. It would be too late to change the temperature of a building a week after receiving the data from the system, after all.
Once you’ve closed the loop with a system, engineers and operators are free to focus on higher-level thinking, problem-solving, and attending to problem assets. They no longer need to analyze the data themselves, input it back to the system, and make decisions and control changes.
Meet Us in the Future of Closed-Loop Controls
The art of the possible with the technology to build, deploy, and scale advanced control applications is far reaching. It impacts both human actions and insights. With tools like Kelvin the future is already here – today you can detect events in real time, augment human intelligence, automate workflows, evaluate options, and then take closed-loop actions.
Closed-loop systems save time, money, and resources. They also reduce human error. Your operators no longer need to focus on mundane, redundant, and sometimes even dangerous tasks. Closed-loop systems also amplify your best engineer’s intelligence, capturing their knowledge the more you run the continuous decision process automation and orchestration software. The result is better and more efficient outcomes.
The pandemic accelerates the need for digital transformation and advanced technologies, with more organizations moving forward on the path toward smart manufacturing. With workforce turnover and staffing challenges abounding in manufacturing, reducing the human load becomes even more important.
Kelvin tools help you meet today’s industrial challenges. From reducing emissions and boosting production yield, to improving human productivity and increasing operational efficiency, our solutions amplify your human resources with artificial intelligence and machine learning.
To learn more about how Kelvin.ai helps customers reduce emissions and hit Net Zero goals — while boosting production and efficiency, contact us today.